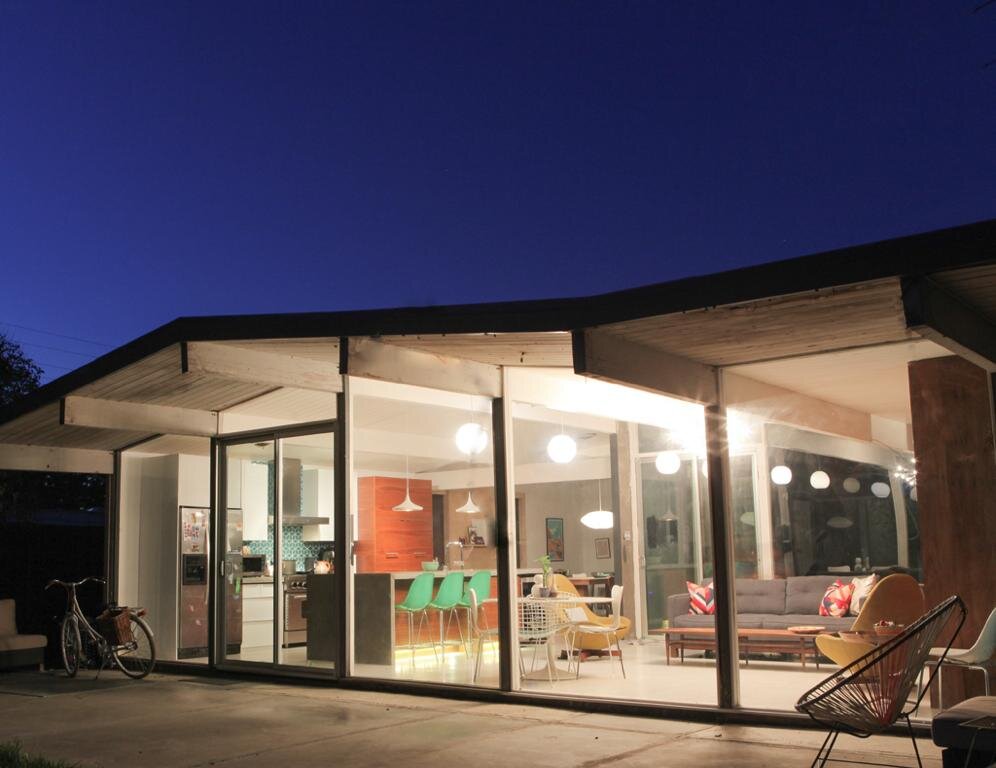
Mid-Century Home Magazine
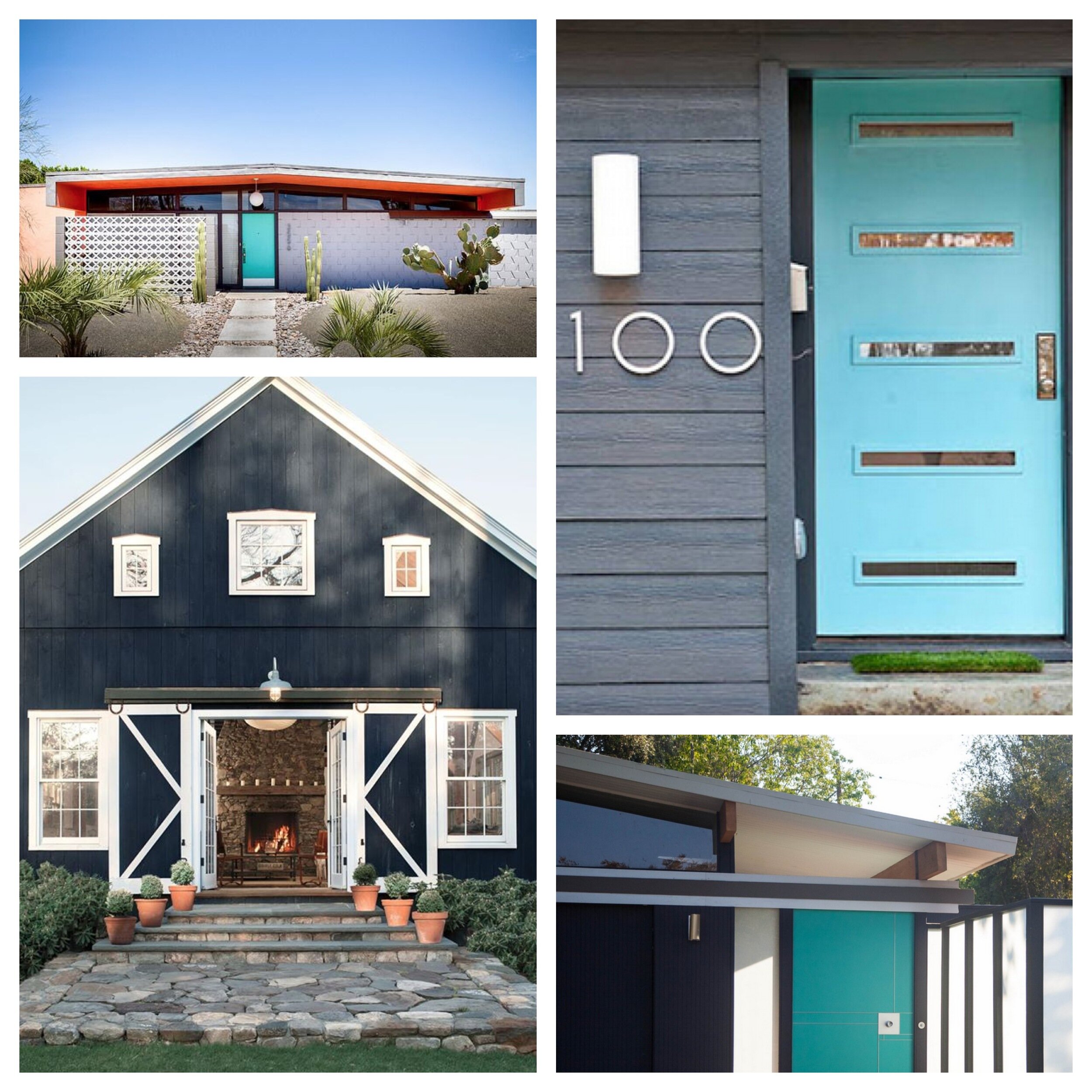
Eichler Exterior Redux
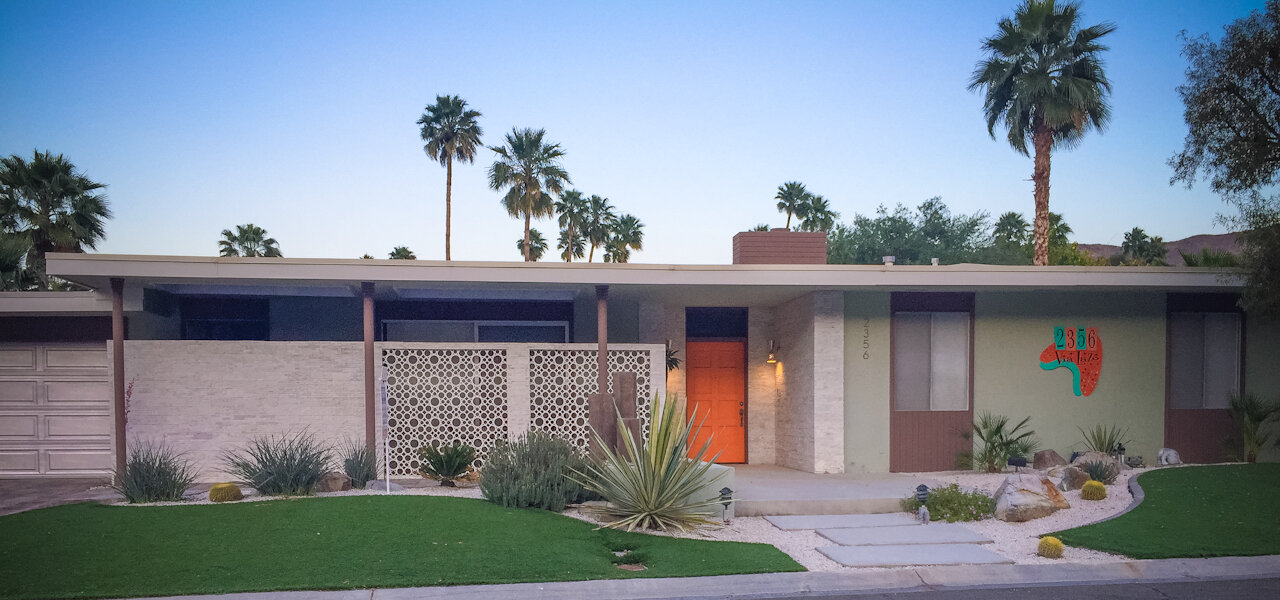
Mid-Century Modern Homes in Palm Springs
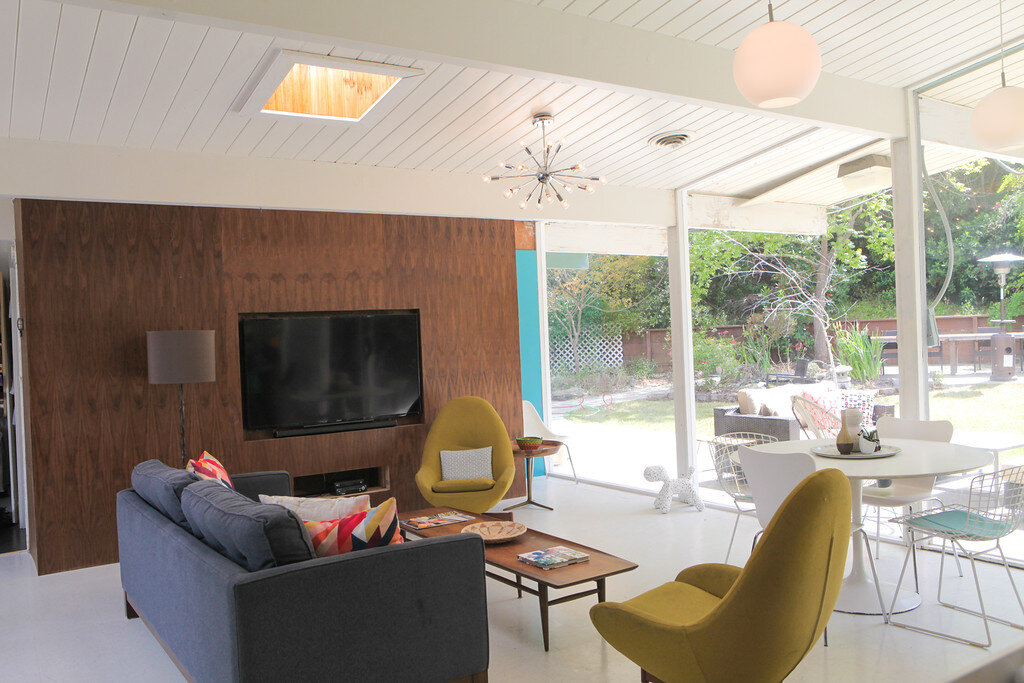
Living Room Remodel: Media Wall, Windows, Closet - 75% Complete
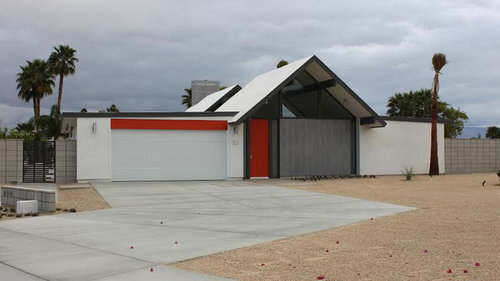
Eichlers on NPR - A historical look back

Eichler Kitchen Remodel - The Final Reveal
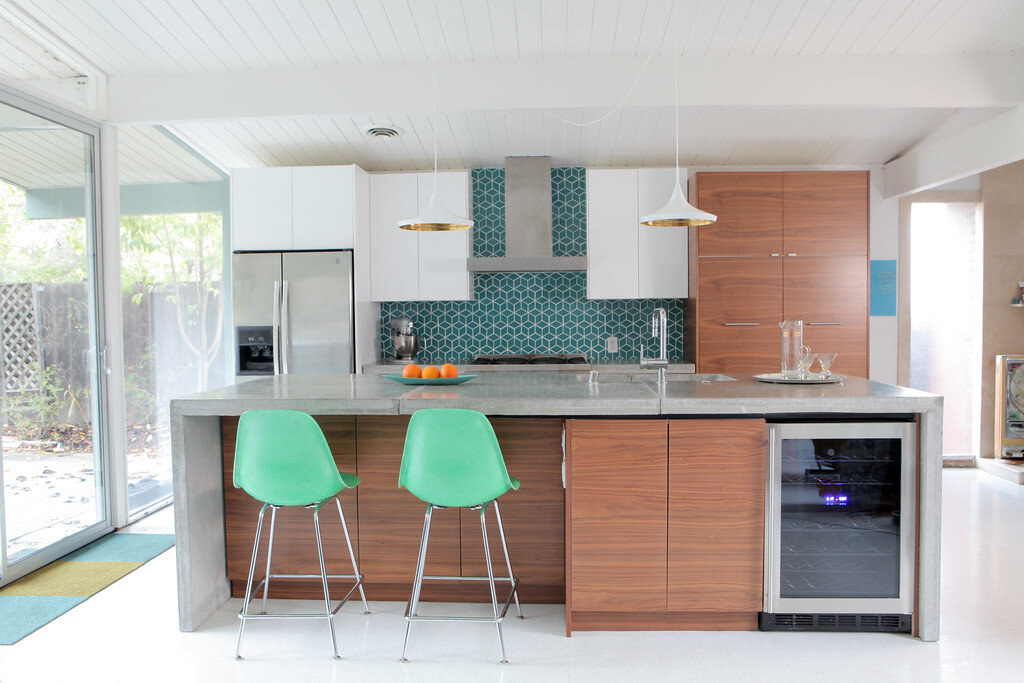
DIY Concrete Countertops
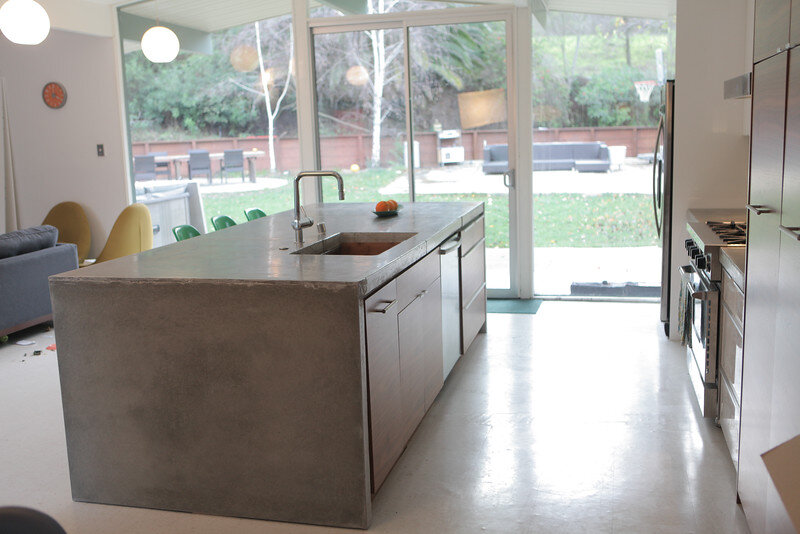
Eichler Sliding Doors: Replacing Patio Doors
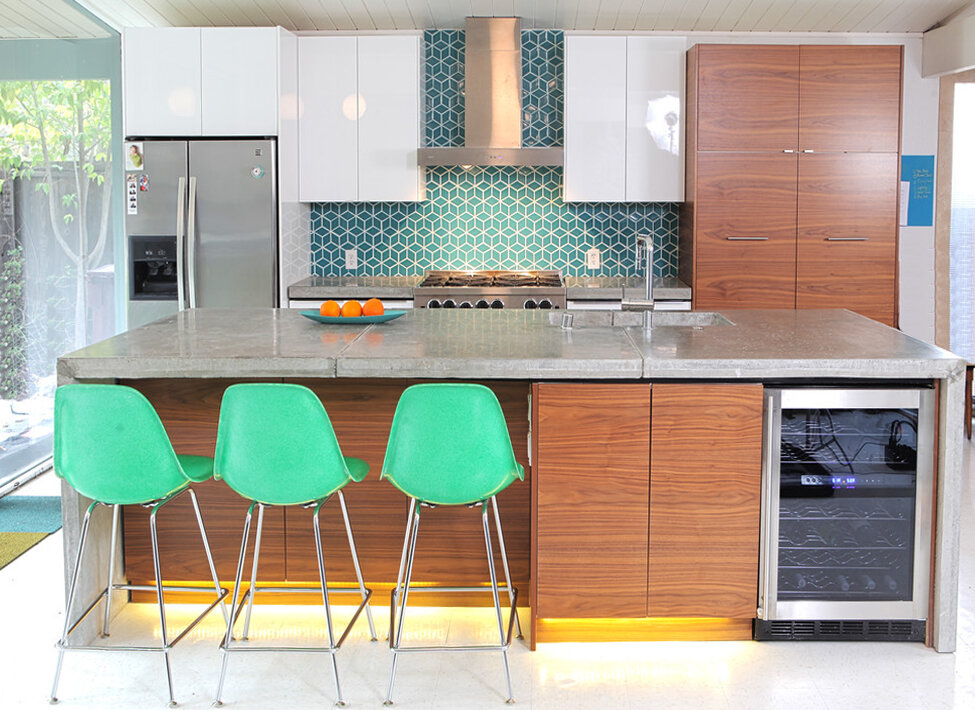
Eichler Kitchen Remodel: Fireclay Tiled Backsplash
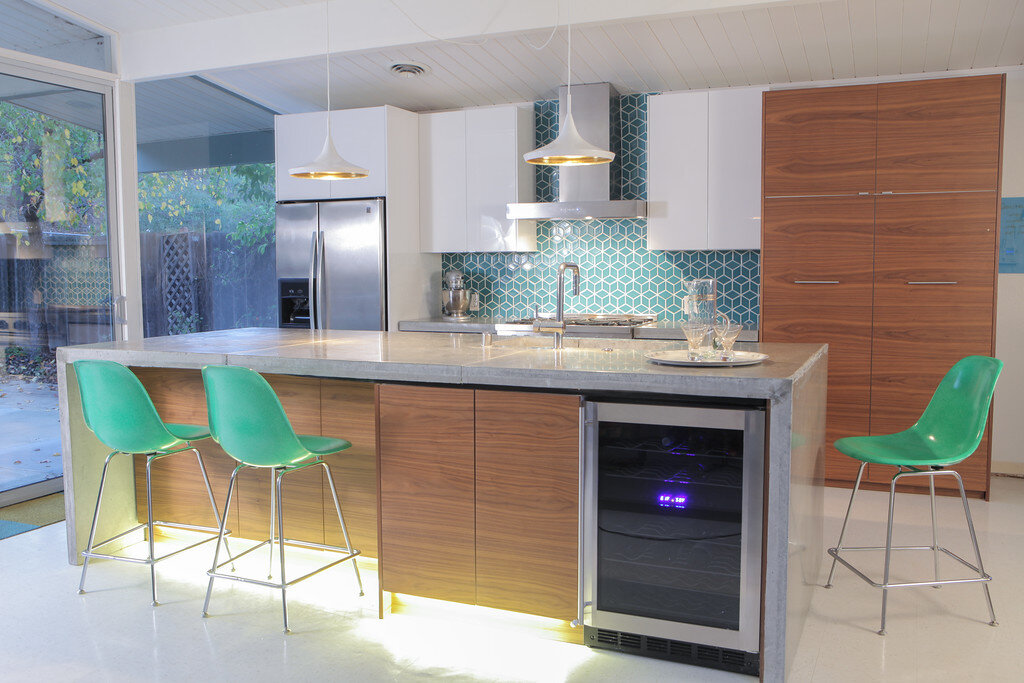
Eichler Kitchen Semihandmade Doors & Panels
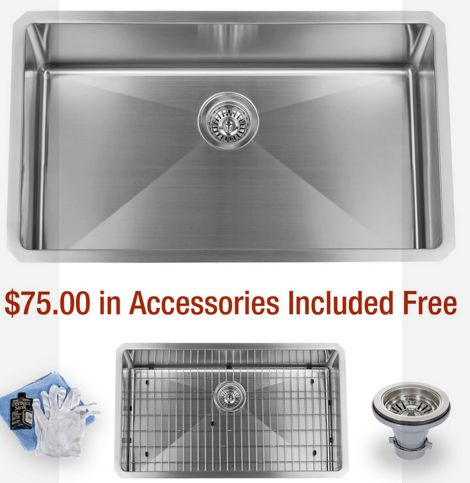
Eichler Kitchen Plumbing & Electrical
Eichler Vent Hood Installation
Karen and John’s Eichler Kitchen Renovation – VCT flooring Installation
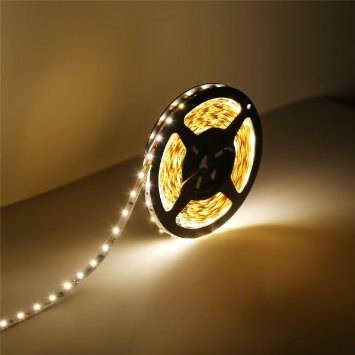
Eichler Kitchen Remodel: LED Toe Kick Lighting
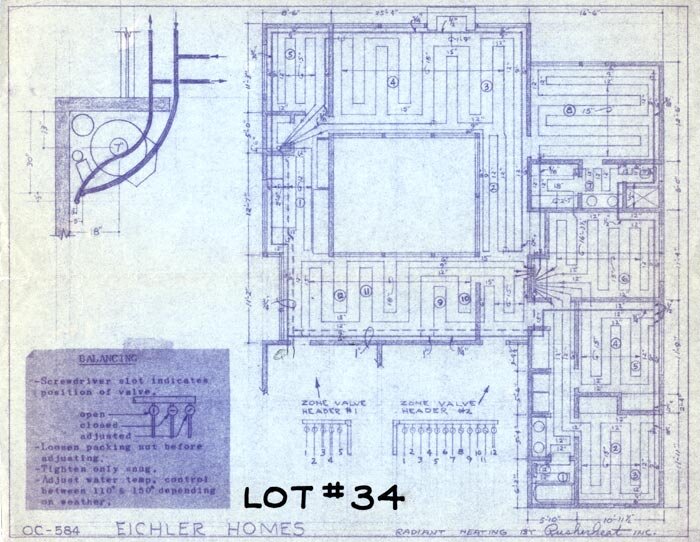
Eichler Radiant Heating Systems
Eichler Flooring
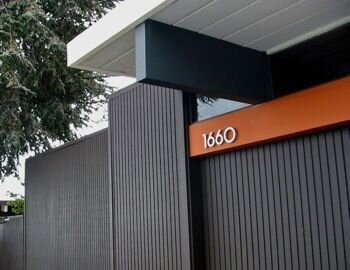
Top 10 Eichler Questions
Honey, we're home!
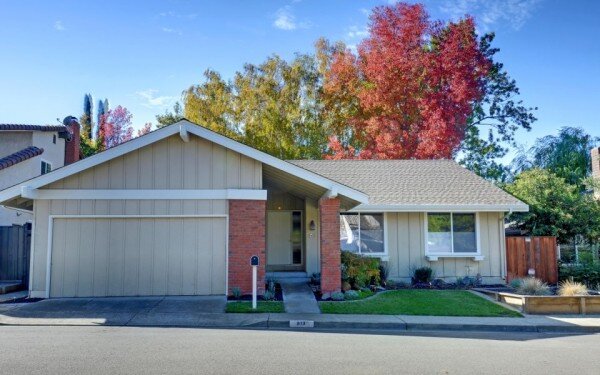